Investigating the influence of yarn characteristics on microfibre release from knitted fabrics during laundering
- School of Design, University of Leeds, Leeds, United Kingdom
Microfibres generated and released during the use and laundering of textiles have been identified as an important source of environmental pollution. The quantity of microfibres released from a fabric can be influenced by several external factors, such as laundering conditions and consumer use, as well as intrinsic factors such as the fibre composition, yarn characteristics, and fabric structure. This study investigates the influence of various yarn characteristics on microfibre release from knitted fabrics as well as exploring the generation of microfibres during the knitting process. Fibre composition and the yarn spinning system has the greatest influence on microfibre release. The greatest quantity of microfibre was released from ring-spun lyocell (1313 ± 140 mg/kg) and the lowest quantity was released from vortex-spun polyester (80 ± 26 mg/kg). The yarn spinning system was also found to have a significant influence, with vortex-spun yarns consistently demonstrating lower microfibre release than corresponding ring-spun yarns, likely due to the reduced hairiness of yarns spun by the vortex system. The importance of fibre damage during the knitting process was also investigated. Several yarns demonstrated significantly greater microfibre release in knitted form compared to loose, hank form, but the scale of difference was found to be dependent on fibre composition.
1 Introduction
Microfibres released from textiles during domestic laundering represent a significant environmental challenge and many studies have reported on their prevalence and associated impacts in the environment (Hurley et al., 2017; Kutralam-Muniasamy et al., 2020; Gaylarde et al., 2021; Liu et al., 2021; Rebelein et al., 2021). The domestic laundering of textiles is considered to be one of the major sources of microfibres (Boucher and Friot, 2017; Carney Almroth et al., 2018; Rathinamoorthy and Raja Balasaraswathi, 2022a), and estimated quantities of microfibre release range from a few thousands (Browne et al., 2011) to several millions of fibres released in every wash (De Falco et al., 2018; Kelly et al., 2019; Kärkkäinen and Sillanpää, 2020; Periyasamy, 2021; Vassilenko et al., 2021) Several studies investigating the factors that influence microfibres released during domestic laundering have begun to focus on the characteristics and properties of different fabrics. These studies have considered the three broad aspects of fabric constructions: fibres, yarns, and fabric structure. Attention has also been given to the formation of microfibres and how this can be reduced, particularly during the textiles manufacturing process. These aspects are reviewed in detail herein.
1.1 Fibre composition
Greater microfibre release has been observed from cellulose-based fabrics than from fabrics constructed of synthetic fibres (Sillanpaa and Sainio, 2017; De Falco et al., 2019a; Zambrano et al., 2019; Cesa et al., 2020; Celik, 2021; Palacios-Marin et al., 2022). This could be due to the higher hairiness of cellulosic fabrics, particularly cotton; the greater number of fibre ends protruding from the fabric surface may result in greater vulnerability to fragmentation of these fibres ends which creates more microfibres (Zambrano et al., 2019). Natural and regenerated cellulose fibres are also generally less durable and more prone to damage than synthetic fibres due to differences in important fibre properties such as strength, elongation, and elastic modulus, which could also lead to increased generation and shedding of microfibres (Sinclair, 2015; Elmogahzy and Farag, 2018; Liu et al., 2023; 2019).
1.2 Yarn characteristics
Yarns spun from staple fibres tend to demonstrate greater microfibre release compared to filament yarns (Carney Almroth et al., 2018; De Falco et al., 2018; Belzagui et al., 2019; Yang et al., 2019; Choi et al., 2021a; Özkan and Gündoğdu, 2021), which can be expected as the shorter length of staple fibres provides them with greater mobility, making them more vulnerable to displacement from the yarn structure. Some level of hairiness is also inevitable in staple spun yarns, meaning more fibre protrusions will be present which could again lead to greater microfibre release. Yarn twist has been identified as an influencing factor, with increased microfibre release reported from woven fabrics comprised of filament yarns with no twist compared to highly twisted filament yarns. The researchers theorised that this was due to limited inter-fibre friction within the yarns with no twist, meaning that the fibres had greater mobility within the yarn structure (Choi et al., 2021a). The influence of different yarn spinning systems was investigated by Jabbar et al. who found greater microfibre release from woven fabrics comprised of conventional ring-spun yarns compared with modified ring-spun yarns indicating that yarn hairiness has a significant impact on microfibre release (Jabbar et al., 2022). The researchers also noted more compact yarns produced by the modified ring spinning systems led to increased inter-fibre cohesive forces, thus reducing the likelihood of microfibre release (Jabbar et al., 2022). Cai et al. found that yarns produced by rotor spinning released more microfibres than corresponding air-jet (also known as vortex) and ring-spun yarns, and even more than the unspun slivers used as the feedstock for yarn spinning. The latter finding suggests the rotor spinning process is possibly damaging individual fibres and creating microfibres through fibre breakage during the opening and/or spinning processes (Cai et al., 2020a). Pinlova et al. also found significantly higher microfibre release from rotor-spun yarns compared to yarns produced by other spinning systems (ring, compact-ring, air-jet) and they noted that production settings in the carding and spinning processes had a significant effect on microfibre release from rotor-spun yarns. For example, four times as much microfibre release was observed when production speeds were increased by 25%, whereas yarns produced by other spinning systems were not as affected by changing production speeds (Pinlova et al., 2022). By contrast, a recent study found both air-jet and rotor-spun yarns released significantly fewer microfibres than ring-spun yarns (Jabbar and Tausif, 2023). The researchers noted that their results for rotor-spun yarns may have differed from previous studies as their testing was conducted on woven fabrics rather than on yarns directly.
1.3 Fabric construction
The tightness or density of the fabric appears to be highly influential, with tighter, more compact fabric structures releasing fewer microfibres than fabrics with a looser, more open construction (De Falco et al., 2019b; Yang et al., 2019; Choi et al., 2021b; Berruezo et al., 2021; Kim et al., 2022; Raja Balasaraswathi and Rathinamoorthy, 2022). The influence of specific fabric structures is less clear; some studies found greater microfibre release from twill weave fabrics compared to plain weave fabrics (Choi et al., 2021b; Berruezo et al., 2021), whilst another reported the opposite (Kim et al., 2022). Berruezo et al. suggested that the compactness of the yarns and the number of interlacing points within the fabric structure were of more importance and provided a better indication microfibre release behaviour than the specific type of weave structure (Berruezo et al., 2021).
By increasing the fabric density, there is an increased number of fibres per unit area which could be expected to result in increasing microfibre release, however the opposite effect has been observed. It has been theorised that in denser fabric structures, there is greater fibre compactness along with reduced fibre mobility. The combination of these factors retains fibres within the yarn and fabric structures, resulting in reduced microfibre release compared to fabrics with more open structures where fibre mobility is higher (Choi et al., 2021b; Berruezo et al., 2021). Additionally, surface treatments and finishes to the fabric could influence the likelihood and quantity of microfibres released. Cai et al. found that fabrics with processed surfaces (fleece, brushed) released on average five times more microfibres than those with unprocessed surfaces, which they deemed unsurprising due to the abrasive forces involved in these surface treatments such as raising, brushing, and cropping, all of which directly create loose fibres and can weaken those which remain (Cai et al., 2020a). However, some surface treatments could reduce microfibre release as they can remove protruding fibres ends which could otherwise be vulnerable to fragmentation and release. For example, treatments such as singeing and biopolishing are sometimes used remove protruding fibre ends thereby reducing hairiness and improving pilling performance. (Ciechañska and Nousiainen, 2005; Tomaney, 2015; Hossain et al., 2021; Kumpikaitė et al., 2021).
1.4 Formation of microfibres during textiles manufacturing
Microfibres are released during the use and/or laundering of textile items, and there is evidence that the abrasive forces and agitation encountered in regular use leads to their formation. However, many of these microfibres may already be present in the fabric before it reaches consumers, as is demonstrated by numerous reports of decreasing quantity of microfibres released in laundering with repeated laundering cycles (Pirc et al., 2016; Sillanpää and Sainio, 2017; Carney Almroth et al., 2018; Belzagui et al., 2019; Kelly et al., 2019; Zambrano et al., 2019; Cai et al., 2020b; Cesa et al., 2020; Lant et al., 2020; Vassilenko et al., 2021; Özkan and Gündoğdu, 2021; Rathinamoorthy and Raja Balasaraswathi, 2022b; Jabbar and Tausif, 2023). This suggests that many microfibres are being formed during the fabric manufacturing and remain loosely held within the fabric structure. These are then readily released during the first domestic laundering cycle. Cai et al. confirmed the presence of microfibres within textiles throughout the manufacturing process, and they also noted that the majority of microfibres were released during the first extraction, and a sharp decrease in the quantity of microfibres released in subsequent extractions (Cai et al., 2020a). Additionally, Jabbar and Tausif investigated the fibre-end morphologies of microfibres released from washing woven fabrics and they found that most fibre damage appeared to have been caused by high-energy loading conditions, indicating that the damage was likely initiated during manufacturing rather than during laundering (Jabbar and Tausif, 2023).
Further work by Pinlova et al. found that microfibres were present prior to yarn production, suggesting that microfibres can be formed as early in the production line as staple fibre preparation (for polyester yarns). They also observed changes in the count and length of fibres extracted at various stages of yarn production, suggesting that more microfibres are being formed throughout the spinning process, however some shorter fibres also appeared to be removed as yarn production progressed (Pinlova et al., 2022).
1.4.1 Learnings from existing knowledge on fibre fly generation
Whilst research into the mechanisms of microfibre formation and release is still emerging, well established textile science can be used to understand the role of fibre, yarn, and fabric characteristics in these mechanisms. In particular, a wealth of research has been conducted into the causes and mechanisms of fibre breakage and fibre shedding that occurs during textile manufacturing processes, shed fibres being referred to as fly, and much can be inferred about microfibre formation and release from this research.
Yarn hairiness has been identified as an important indicator of fly generation during knitting and weaving (Wang, 1999; Koo, 2003; Majumdar, 2010). The amount of fibre fly generated has been observed to decrease as the mean fibre length increases, and as yarn twist increases (Ruppenicker and Lofton, 1979; Barella et al., 1989; Lawrence and Mohamed, 1996; Huh et al., 2002; Yuksekkaya, 2010). As well as reducing hairiness, longer fibre lengths lead to greater frictional forces and therefore improved cohesion between fibres within the yarn (Lawrence and Mohamed, 1996; Yuksekkaya, 2010). Increasing the twist also generates greater frictional forces within the fibre assembly and significantly reduces hairiness, especially the length of fibre protrusions, as fibre ends are better incorporated into the yarn body as twist levels increase (Barella, 1957; 1956; Barella et al., 1989; Behery, 2005; Majumdar, 2010).
The linear density of the fibres within the yarn can also influence the amount of fibre fly generated. For yarns with the same linear density but spun from fibres with different fineness, there will be more fibres within the cross-section of yarns made from finer fibres than those with coarser fibres (see Figure 1). More fibres in the cross-section can create more surface hairs and loose fibres which can lead to more fibre fly (Yuksekkaya, 2010). However, more fibres in the yarn cross-section can also provide increased friction and cohesion thereby reducing fibre fly (Lawrence and Mohamed, 1996).
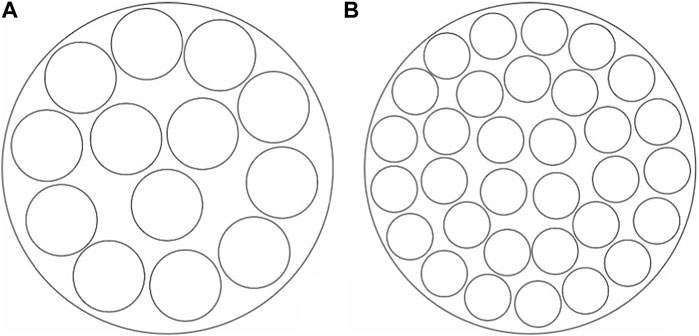
Figure 1. Representation of yarn cross-section for yarns of the same linear density comprised of (A) coarser fibres, and (B) finer fibres.
Fibre regain, or moisture content can also impact the level of fly generation, particularly for natural fibres. Increased moisture content has been noted to reduce fibre fly generation as it causes fibre swelling, which increases inter-fibre friction and cohesion (Lawrence and Mohamed, 1996; Yuksekkaya, 2010). This effect may be even more pronounced for natural cellulose fibres such as cotton as they demonstrate increased tensile strength in wet conditions (Miyake et al., 2000).
In knitted fabric production, increased fibre fly is observed when knitting tighter fabrics due to greater friction and abrasion between the yarns and knitting machine components, such as yarn guides and needles, as well as between the yarns themselves (Ruppenicker and Lofton, 1979; Buhler et al., 1988; Lawrence and Mohamed, 1996).
1.5 Investigating fibre and yarn characteristics impact on microfibre release
While there are many influencing factors, this study focuses on investigating the influence of fibre composition, yarn-spinning system, and yarn linear density on the quantity of microfibre released from knitted fabrics during simulated laundering. Additionally, it explores the importance of the manufacturing process in generating microfibres, informed by the existing knowledge of fibre fly generation in the knitting process specifically. This has been achieved by comparing yarns in hank form (coils of yarn with no defined structure), to yarns which had been knitted into fabric samples.
2 Materials and methods
2.1 Materials
A range of commercially available staple spun yarns were sourced to explore the impact of fibre composition, yarn linear density, and spinning system on microfibre release. These included: polyester and cotton yarns in both 15 tex and 30 tex, spun by vortex and conventional ring spinning systems (PET-30-vortex, PET-30-ring, PET-15-vortex, PET-15-ring, COT-30-vortex, COT-30-ring, COT-15-vortex, COT-15-ring); viscose, modal, low-fibrillation lyocell, and regular lyocell yarns of 15 tex which were compact-ring spun (VIS-ring, MOD-ring, LYO-LF-ring, LYO-reg-ring); and acrylic yarns with 0.9 dtex and 1.3 dtex fibre linear density, and 20 tex yarn linear density from rotor spinning system (ACR-0.9, ACR-1.3). All yarns were undyed, thus removing the influence of wet processing. The yarn details are provided in Table 1. The yarn linear density was confirmed by testing according to ISO 2060:1995 (British Standards Institution, 1995), and expressed as tex according to ISO 1144:2016 (British Standards Institution, 2016); grams per kilometre of yarn.
2.2 Yarn winding method
Yarn hanks were formed to assess microfibre release from the yarns without the influence of fabric structure. The yarn hanks were formed using a yarn wrap reel (HY086C Electronic Yarn Wrap Reel, Anytester) to unwind set lengths of yarn from the yarn packages. To ensure easy comparisons of microfibre results between the different yarn linear densities and fabrics, the length of yarn used to form the hanks was adjusted depending on the yarn linear density. Hanks were formed of either 550 m for yarns with linear densities of 15 or 20 tex, and 225 m for yarn linear densities of 30 tex. This adjustment was made to ensure that a comparable mass of yarn was tested in each case.
For each yarn, eight yarn hanks were created, which were prepared for microfibre release testing by oven-drying at 50°C for a minimum of 4 h, after which the mass of each oven dried hank was recorded to an accuracy of 0.0001 g (ADA 210 Balance, Adam Equipment Co., Ltd., Capacity: 210 g, Readability: 0.0001 g).
2.3 Knitting method
Fabrics were knitted from the test yarns using a manual V-bed knitting machine (FS-NHF4, Dubied). The machine gauge was 12 knitting needles per inch and the loop tension was set at nine for all cams (cams traverse along the needle bed and control the action of the knitting needles). All active needles on both beds were knitted together, forming a double jersey knitted structure.
The density or coverage of knitted fabrics is determined by the machine gauge and the linear density of the yarn. To form knitted fabrics with comparable densities from all test yarns, coarser yarns with linear density of 30 tex were knitted with a single end of yarn, and finer yarns with linear densities of 15 or 20 tex were knitted with two ends of the same yarn. In this case, the two ends of the same yarn were fed through the knitting machine simultaneously, without folding or twisting the yarns together. This approach ensured that the knitted structure and stitch density were as comparable as possible for all samples. An example of the fabrics produced by each knitting method is shown in Figure 2. The stitch density is defined as the number of stitches in a square inch of fabric, calculated as the number of wales (vertical columns of loops) per inch multiplied by the number of courses (horizontal rows of loops) per inch. Details of all the knitted fabrics are provided in Table 2.
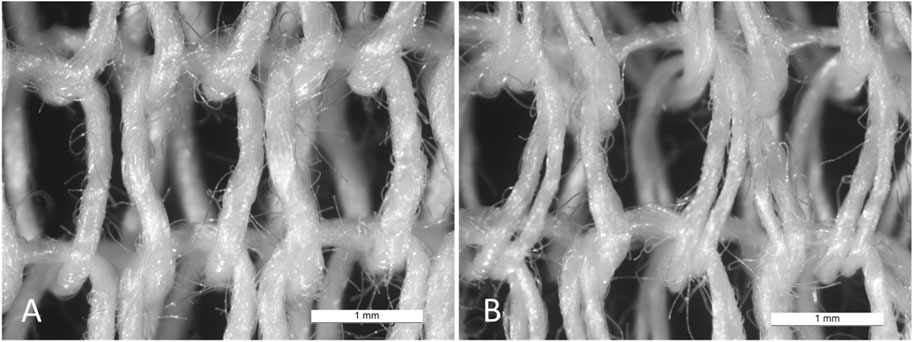
Figure 2. Comparison of knitted fabric structure for (A) PET-30-vortex with one yarn end, and (B) PET-15-vortex with two yarn ends to achieve comparable stitch densities (images taken before laundering).
For each yarn, a minimum of eight test fabrics were knitted with a specimen size of approximately 290 × 150 mm. The outer edges of the specimens were hemmed with a double-rolled hem approximately 1 cm wide and secured by sewing a lockstitch around the perimeter of the specimen using nylon filament sewing thread in preparation for microfibre release testing. After oven-drying at 50°C for a minimum of 4 h, the mass of each fabric specimen was recorded to an accuracy of 0.0001 g (ADA 210 Balance, Adam Equipment Co. Ltd., Capacity: 210 g, Readability: 0.0001 g). These lengths of yarns correspond with the approximate length and mass of yarn required to create the knitted samples. This ensured that the amount of yarn tested in hank form and knitted form was comparable.
2.4 Microfibre release method
The mass of microfibre released from the yarn hanks and knitted fabrics was tested according to the method described by Tiffin et al. (Tiffin et al., 2022) which is equivalent to ISO 4484-1:2023 (British Standards Institution, 2023). Specimens were laundered using a simulated laundering device (Gyrowash 1615/8, James Heal) in canisters containing 360 mL distilled water (without detergent) and 50 stainless steel ball bearings, at 40°C for 45 min.
After laundering, the test liquor from each specimen was collected in glass beakers and the samples and all canister components were rinsed thoroughly to ensure all released fibres were captured. The test liquor was then filtered through 1.6 µm glass microfibre filter papers (Whatman Grade GF/A Glass Microfiber Filters) using vacuum assisted single-stage filtration (16309 All-glass vacuum filter holder, Sartorius Stedim). The oven-dry mass of the filters immediately before and after testing (dried at 50°C for a minimum of 4 h) was compared to determine the mass of microfibre released relative to the initial mass of the test specimen, expressed as mg/kg. Results given represent the mean microfibre release (mg/kg) and the error reported is the 95% confidence interval. Two-tailed t-tests and one-way ANOVA tests were used to assess the significance of results, and an alpha level of .05 was used for all statistical tests.
3 Results and discussion
3.1 Microfibre release from yarn hanks
All yarn samples were tested in loose hank form to provide a baseline set of results for microfibre release. The microfibre release from the hanks of each yarn sample is shown in Figure 3. ACR-1.3 released the greatest mass of microfibre in hank form (538 ± 217 mg/kg), whilst COT-30-vortex released the lowest mass of microfibre in hank form (163 ± 42 mg/kg). Generally speaking, regenerated cellulosic yarns and acrylic yarns demonstrated greater release of microfibres than the cotton and polyester yarns tested, however this is without considering differences in the spinning systems and direct comparisons of the influence of fibre composition are not possible here for this reason. Where comparisons could be made between yarn spinning system and yarn linear density for the cotton and polyester yarns, the results were not consistent and there is no clear trend for either vortex or ring spun yarns, nor 30 tex or 15 tex yarns performing favourably in terms of their microfibre release in hank form. However, for the cotton and polyester yarns, there is a clear influence of fibre composition, with all polyester yarns releasing greater quantities of microfibre compared to the corresponding cotton yarns when tested in hank form (p < .001 in all cases).
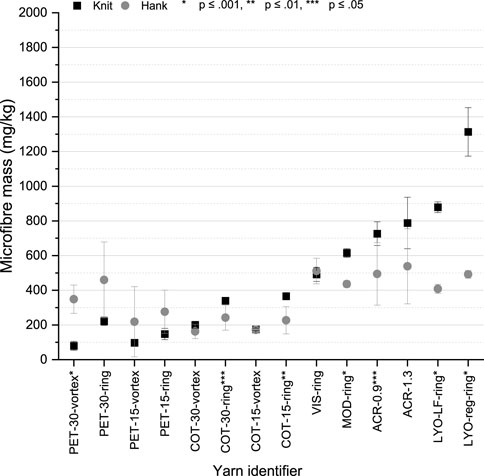
Figure 3. Mass of microfibre released after laundering for different yarns in hank (loose yarn bundle) and knitted form (error bars represent 95% confidence interval, p-values indicate statistical significance of difference between knit and hank samples, determined by two-tailed t-test).
3.2 Influence of knitting process and fabric structure
To investigate the influence of fabric structure on microfibre release, the same yarns were tested in the knitted form described earlier. Much of the literature relating to the fabric structure and microfibre release has established a negative correlation between the density or tightness of the fabric and the quantity of microfibre released, with tighter constructions releasing less microfibre overall (De Falco et al., 2019b; Yang et al., 2019; Choi et al., 2021b; Berruezo et al., 2021; Kim et al., 2022; Raja Balasaraswathi and Rathinamoorthy, 2022). It was therefore theorised that the loose, unstructured hanks of yarns would release more fibre during laundering than in knitted, structured form. Results for the mass of microfibre release from hanks compared to knitted samples are shown in Figure 3 and Table 3.
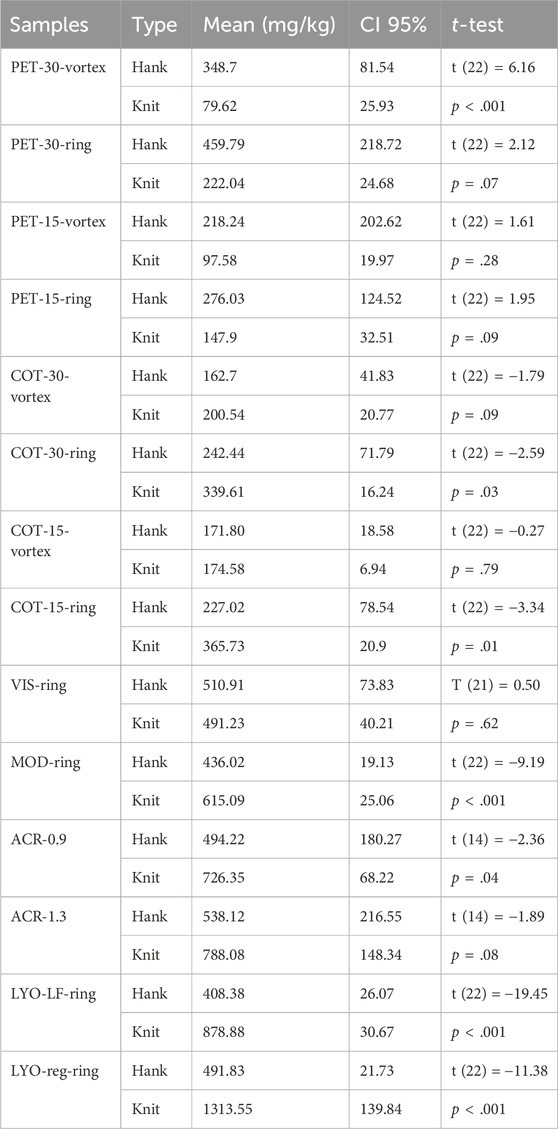
Table 3. Mass of microfibre released after laundering for different yarns in hank and knitted form - statistical analysis by two-tailed t-test (alpha level .05).
However, the results showed that in most cases the yarn hanks released significantly less fibre than the knitted fabrics (COT-30-ring, COT-15-ring, MOD-ring, ACR-0.9, LYO-LF-ring, LYO-reg-ring), or there was no statistically significant difference between the two structure types (PET-30-ring, PET-15-ring, PET-15-vortex, COT-30-vortex, COT-15-vortex, VIS-ring, ACR-1.3), as determined by two-tailed t-test. Only one sample, PET-30-vortex, showed a statistically significant increased rate of microfibre release from the yarn hank compared to its knitted form (hank (349 ± 82 mg/kg) to knit (80 ± 26 mg/kg), t (22) = 6.16, p < .001).
Analysis of the difference in release between the hank and the knitted fabric forms suggested a dependency on fibre composition, as none of the polyester samples demonstrated statistically significantly increases in microfibre release in the knitted form. This may be due to polyester’s superior strength and durability properties. Additionally, the influence of spinning system can be noted as none of the vortex-spun samples released significantly greater microfibre release in knitted form, which could be explained by vortex-spun yarns having lower hairiness than ring-spun yarns, possibly owing to the wrapper fibres in the yarn structure (Patnaik et al., 2007).
Reduced microfibre release from hanks could be explained by considering the frictional and abrasive forces associated with the process of forming the yarn hanks compared to the process of forming the knitted samples. A schematic of the process for forming the yarn hank on a wrap reel is shown in Figure 4, which shows the number of points of contact between the yarn and yarn guides. There is little tension applied to the yarn as it is wound to ensure the resultant yarn hank remains loose enough to be easily removed from the wrap reel without damage to the yarn. The yarn path is relatively simple, and all the contact points are also relatively smooth, meaning that the abrasive forces between yarn and contact points are relatively low.
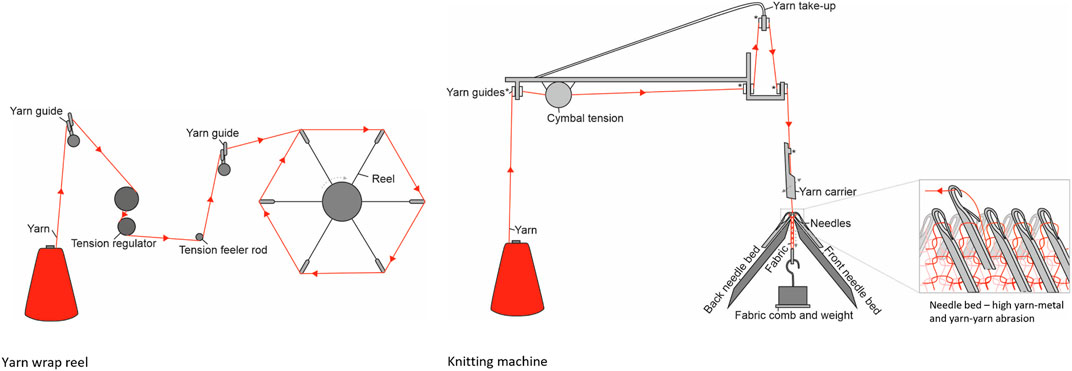
Figure 4. Yarn path comparison (not to scale) - yarn wrap reel and knitting machine (moving parts indicated by dashed lines).
By contrast, the yarn path for knitting is more complex and includes steeper yarn angles and more machine elements which the yarn contacts. A schematic of the knitting process is shown in Figure 4. The yarn passes through multiple ceramic guides and the tension is controlled as the yarn proceeds to the knitting needles. In the knitting zone, the yarn carriage passes the yarn feeder across the needles as they raise and lower in turn, and the needle latches catch and pull the yarn through the loop created in the previous row. In this portion of the process there is significant shearing forces between the yarn and the needle as the needle is raised and lowered through the yarn loops (Ruppenicker and Lofton, 1979). There is also considerable frictional force acting between the yarn loops themselves (yarn on yarn abrasion) as the newly formed loop is pulled through the previously formed loop (Lawrence and Mohamed, 1996). As the fabric forms, it is also held under tension by the addition of weights to ensure each row of loops is lowered away from the hooked ends of the needles so a new row can be formed. This additional tension can add to the abrasive forces acting between the yarn loops. The knitting process is well known to cause fibre damage, and airborne fibre fly is common in commercial knitting factories. It can therefore be inferred that the abrasive forces experienced during the knitting process, caused some fibre breakage, and contributed to the generation of microfibres which were released during our laundering testing.
These results indicate that the relationship between fabric structure and microfibre release is also influenced by the mechanical action and potential fibre damage present within manufacturing processes. It should also be noted that in the present study, knitting was conducted on a small-scale with the yarn carriage operated manually at relatively low speeds. In larger-scale production, the knitting process is typically automated and conducted at higher speeds and with more contact points. Increased knitting speed has been found to cause more fibre damage (Ruppenicker and Lofton, 1979; Lawrence and Mohamed, 1996), which could lead to more microfibre generation and release from full-scale production fabrics than has been reported here. In addition, while it has been found that fabric structures which are tighter and denser reduce microfibre release, it is also known that more fibre fly (i.e., fibre breakage) is generated during the production of tighter knitted fabrics (Ruppenicker and Lofton, 1979; Buhler et al., 1988; Lawrence and Mohamed, 1996). It could be that the additional fibre fragments generated whilst knitting tighter structures are still better retained within the fabric due to its tightness, however this could affect the long-term microfibre release behaviour as these fibre fragments can eventually become detached through use and laundering over the lifetime of the textile item. Conversely, it could be the case that the additional fibre fragments generated when knitting tighter fabrics are more efficiently removed during the knitting process (as airborne fibres or fibre fly, which is often removed during production to prevent loose fibres collecting and causing machine faults) and therefore there are fewer manufacturing-generated fibre fragments present in tighter fabrics compared to looser fabrics. Additional research would be required to confirm which, if either, of these factors is most relevant for microfibre release.
3.3 Influence of yarn characteristics
The influence of several different yarn characteristics was investigated further by comparing the mass of microfibre released from knitted samples. Characteristics explored included yarn linear density (15 tex and 30 tex), yarn fibre composition (polyester and cotton), and yarn spinning system (ring spinning and vortex spinning). These results are shown in Figure 5.
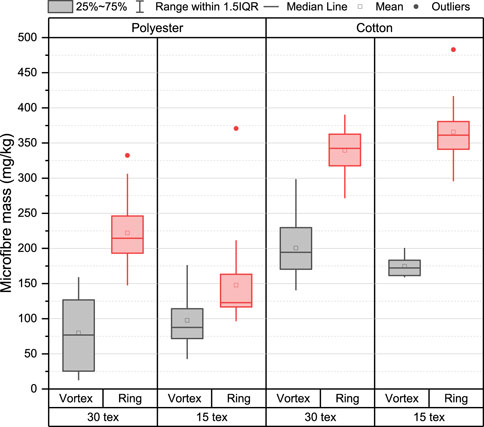
Figure 5. Mass of microfibre released after laundering for yarns of different spinning system (vortex or ring), linear density (30 tex or 15 tex), and fibre composition (polyester or cotton) (tested as knitted fabric samples).
3.3.1 Influence of yarn spinning system
The mass of microfibre released from vortex-spun yarns was significantly lower than the corresponding ring-spun yarns in all cases as determined by a two-tailed t-test. These results are in agreement with other studies which have reported lower microfibre release from air-jet/vortex spun yarns when compared with conventional ring spinning (Pinlova et al., 2022; Jabbar and Tausif, 2023).
Unlike ring spun yarns, vortex spinning introduces twist predominantly to fibres at the yarn surface, by a vortex created by jets of air. The resultant yarn structure consists of mostly parallel fibres in the yarn core with a sheath of twisted wrapper fibres at the yarn surface (Elhawary, 2015). This yarn structure could limit fibre fragmentation and release of fibres from the core section as the wrapper fibres protect them from abrasion and damage. Additionally, vortex-spun yarns are characterised by low hairiness relative to ring spun yarns, which could also be attributed to the presence of wrapper fibres (Patnaik et al., 2007), and hairiness has been identified as an important factor in microfibre release by several works (Zambrano et al., 2019; Özkan and Gündoğdu, 2021). Pinlova et al. also observed that the hairiness of their air-jet spun yarns was mostly formed of fibre loops with the fibre ends incorporated back into the yarns rather exposed fibre ends, which they suggested could indicate greater entanglement which would result in few fibres being released (Pinlova et al., 2022). The difference in hairiness between the ring spinning and vortex spinning systems for the polyester yarns tested is shown in Figure 6. A greater number and length of protruding fibres can be seen on the yarn surface for the ring-spun yarn, and the difference in hairiness is also notable in the knitted fabric samples, with more fibres visible in the gaps between the knitted loops in the ring-spun example.
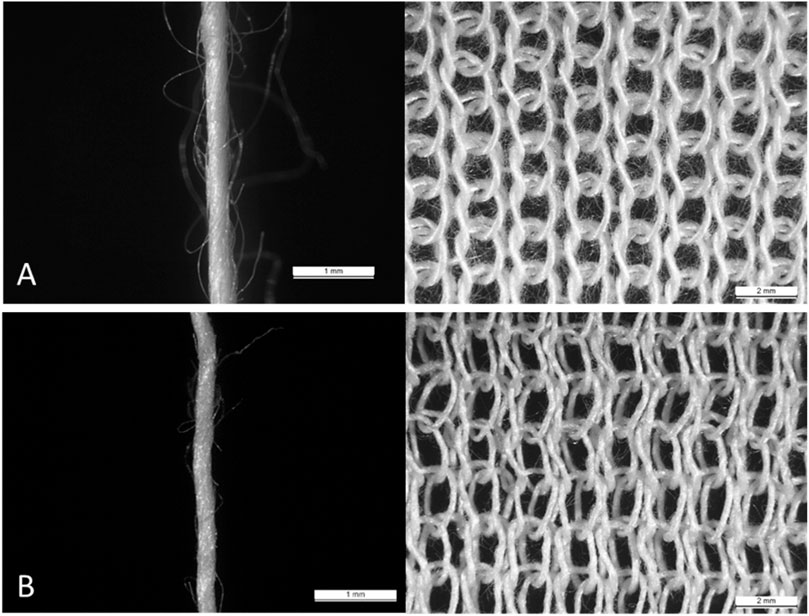
Figure 6. Comparison of yarn hairiness for yarns of the same linear density (30 tex) and different spinning systems (ring or vortex). (A) PET-30-ring and (B) PET-30-vortex (images taken before laundering).
3.3.2 Influence of yarn linear density
The influence of yarn linear density on microfibre release from the knitted fabrics is less clear for the yarns tested. However, in the cases where a difference was noted, the finer 15 tex yarns released less microfibre than the coarser 30 tex yarns. For example, the COT-15-vortex released significantly less microfibre than the equivalent 30 tex yarn (COT-30-vortex: 201 ± 21 mg/kg, COT-15-vortex: 175 ± 7 mg/kg (t (30) = 2.32, p = .03)). Similarly, the microfibre release was significantly lower from PET-15-ring than PET-30-ring (PET-30-ring: 222 ± 25 mg/kg, PET-15-ring: 148 ± 33 mg/kg (t (30) = 3.56, p = .001)).
For the ring-spun cotton yarns and the polyester vortex-spun yarns, there were no significant differences in microfibre release between the 15 tex and 30 tex yarns (COT-30-ring to COT-15-ring, t (30) = −1.93, p = .06; PET-30-vortex to PET-15-vortex, t (30) = −1.08, p = .29).
The 15 tex yarns were knitted with two yarn ends, but the yarn ends were not twisted together. By using two ends of the finer yarn, the difference in knitted structure and tightness between the 30 tex yarns and 15 tex yarns was limited as far as possible. The influence of the linear density on microfibre release has not been previously reported to the knowledge of the authors. However, these results are consistent with the literature relating to fibre shedding or fibre fly generation in processing. There are some conflicting reports on the influence of yarn linear density on fibre fly generation (Ruppenicker and Lofton, 1979; Lawrence and Mohamed, 1996), and some researchers found the linear density to have no significant influence (Oxtoby, 1963; Ruppenicker and Lofton, 1979; Lawrence and Mohamed, 1996) however, greater fibre shedding has been noted from coarser yarns (higher yarn linear density/tex value) than for finer yarns for the same yarn length (Basu and Gotipamul, 2003). Coarser yarns are generally found to be more hairy than fine yarns, partly due to a greater number of fibres in the yarn cross-section meaning there is a statistically greater likelihood of protruding fibre ends (Barella, 1983; Das, 2004; Krupincová and Meloun, 2013). A difference in hairiness between the 30 tex and 15 tex yarns tested could account for the instances where the finer yarns released fewer microfibres than the coarser yarns, despite two ends of the finer yarns being incorporated into the knitted samples.
3.3.3 Influence of fibre composition
The influence of fibre composition was first explored by comparing cotton and polyester yarns in knitted form. The mass of microfibre released from the polyester fabrics was significantly lower than equivalent cotton yarns irrespective of spinning system and yarn linear density, as determined by a two-tailed t-test. The lower release observed from polyester yarns compared to cotton is likely due to differences in fibre tensile properties. Polyester fibres are generally stronger than cotton fibres, having greater tensile strength and superior breaking elongation and elastic modulus (Sinclair, 2015; Elmogahzy and Farag, 2018; Liu et al., 2023), and these properties are considered to be important determining factors for microfibre generation and release (Liu et al., 2023; 2021; 2019). Polyester is therefore more durable and less prone to fibre damage during both the knitting and laundering processes which could lead to microfibre generation.
Additionally, polyester yarns generally have lower hairiness than cotton yarns, and reduced hairiness has been observed in cotton/polyester blended yarns as the polyester content increases (Canoglu and Tanir, 2009). The difference in hairiness between the ring-spun cotton and polyester tested here is shown in Figure 7. Considerably more fibre protrusions can be observed on the cotton yarn and these protruding fibres are also of longer length than those on the polyester yarn.
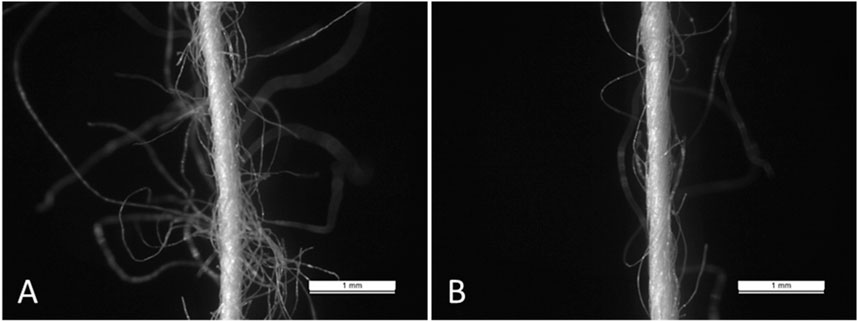
Figure 7. Comparison of yarn hairiness for yarns of the same linear density (30 tex) and different fibre compositions (cotton or polyester). (A) COT-30-ring and (B) PET-30-ring (images taken before laundering).
The influence of fibre composition was further explored by comparing a selection of 15 tex, ring-spun yarns in knitted form: PET-15-ring, COT-15-ring, VIS-ring, MOD-ring, LYO-LF-ring, and LYO-reg-ring. Results for the mass of microfibre release can be found in Figure 8. PET-15-ring demonstrated the lowest amount of microfibre release (148 ± 33 mg/kg), with all cellulose-based yarns having greater release than polyester, and regenerated cellulose yarns having greater release than cotton. A one-way ANOVA test was performed to compare the effect of fibre composition on microfibre release and revealed that there was a statistically significant difference in microfibre release between at least two groups (F (5, 89) = [161.11], p = < .001). Tukey’s test for multiple comparisons found no statistically significant difference between COT-15-ring and VIS-ring (p = .09), or between VIS-ring and MOD-ring (p = .10). The difference in microfibre release between all other fibre composition was statistically significant (p < .01 in all cases).
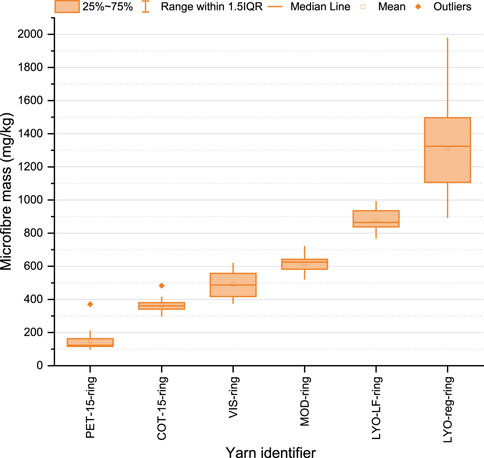
Figure 8. Mass of microfibre released after laundering from 15 tex, ring-spun yarns of different fibre compositions (polyester, cotton, viscose, modal, and lyocell (low-fibrillation and regular)) (tested as knitted fabric samples).
LYO-reg-ring released the largest quantity of microfibre and also demonstrated the greatest variability in results between specimens (1313 ± 140 mg/kg). This high level of microfibre release could be due to lyocell fibre’s known tendency for fibrillation (Lenz et al., 1993; Hearle, 2001; White, 2001). Fibrillation refers to the longitudinal splitting of fibre into microfibrils (White, 2001; Goswami et al., 2009) and is a common phenomenon in regenerated cellulosic fibres (Moriam et al., 2021; Graupner et al., 2023). Lyocell fibres are particularly vulnerable to fibrillation due to their fibrillar structure. Lyocell fibres have a higher degree of crystallinity than other regenerated cellulose fibres, with highly oriented crystallites aligned parallelly to the fibre axis (Fink et al., 2001; Michud et al., 2016). However, the lateral connections between the crystallites are weak and can be easily broken, especially under wet abrasion conditions (Mortimer and Péguy, 1996; Udomkichdecha et al., 2002; Zhang et al., 2006). This leads to localised separation of crystallites at the fibre surface, leaving partially detached fibrils and a hairy appearance (Parajuli et al., 2021; Sharma et al., 2021; Graupner et al., 2023).
Other regenerated cellulose fibres such as modal and viscose have lower crystalline orientation due to differences in the manufacturing process, and therefore demonstrate limited tendency to fibrillate relative to lyocell (Mortimer and Peguy, 1996; Moriam et al., 2021; Graupner et al., 2023). While fibrillation can be advantageous for certain applications, it can also make lyocell more difficult to process than other regenerated cellulose fibres and can lead to excess pilling if not properly controlled (Goswami et al., 2009). Fibre fibrillation could be contributing to the increased microfibre release demonstrated by both lyocell samples, relative to the other fibre compositions, as protruding fibre ends can be easily fibrillated under the mechanical action and wet conditions of laundering, leaving many small fibre fibrils vulnerable to breakage and detachment.
There was also a difference in the quantity of microfibre released from the two different lyocell samples. LYO-LF-ring is a “low fibrillation” lyocell and the fabrics knitted from this yarn released significantly less microfibre mass than the regular lyocell yarn, LYO-reg-ring (LYO-LF-ring: 879 ± 31 mg/kg, LYO-reg-ring: 1313 ± 140 mg/kg (t (30) = −5.95, p < .001)). This further supports the theory that fibrillation is contributing to increased microfibre release.
It should also be noted that the regenerated cellulose samples (VIS-ring, MOD-ring, LYO-LF-ring, LYO-reg-ring) were manufactured by a compact-ring spinning system, whereas the polyester and cotton samples (PET-15-ring and COT-15-ring) were produced by conventional-ring spinning. Conventional-ring spun yarns have been demonstrated to release a significantly greater quantity of microfibre than compact-ring spun yarns due to differences in hairiness between the yarns produced by each spinning systems, as well as improved inter-fibre cohesion in the compact-ring spun yarns (Jabbar et al., 2022). This suggests that the relative differences between the microfibre release of regenerated cellulose compared to cotton and polyester could be underestimated in the present work.
3.3.4 Influence of fibre linear density
The influence of fibre linear density on microfibre release was analysed for the acrylic yarns. Both yarns were produced by the rotor spinning system and to the same yarn linear density, with the only difference being the fineness of the constituent fibres. ACR-0.9 and ACR-1.3 were comprised of fibres of 0.9 dtex and 1.3 dtex (1 dtex (decitex) = 0.1 tex), respectively. The results for microfibre release from the acrylic yarns when tested as knitted fabrics demonstrated slightly lower release from ACR-0.9 (726 ± 68 mg/kg) than from ACR-1.3 (788 ± 148 mg/kg), however the difference was not statistically significant as determined by a two-tailed t-test (t (14) = −0.74, p = .047). As the yarn linear density is the same for both yarns, ACR-0.9, will have more fibres in the yarn cross-section than ACR-1.3. It has been suggested that a greater number of fibres in the yarn cross-section can contribute to increased cohesion and friction between the fibres, resulting in a reduction in fibre-fly (Lawrence and Mohamed, 1996). This could also explain the slight reduction in microfibre release from the acrylic yarn comprised of finer fibres.
4 Conclusion
Comparing the microfibre release of yarns in both hank and knitted form demonstrated the important influence of fibre damage during the knitting process, with several yarns having significantly greater microfibre release after being knitted. This scale of damage and therefore microfibre release is dependent on fibre composition, with fibres that are characterised by high strength, such as polyester, seeming to be less affected by the knitting process than other fibre types which have lower strength profiles such as cotton and regenerated cellulose. These findings demonstrate that microfibre generation occurs during the textile production process and therefore testing for microfibre release at intermediate stages of production is not likely to be reflective of the microfibre release performance of the finished product.
Regenerated cellulose yarns also performed significantly worse than cotton yarns, and lyocell yarns demonstrated the greatest microfibre release of all yarns and fabrics tested. This is likely due to their well-documented tendency to fibrillate when abraded in wet conditions. Yarn spinning system was also found to have an important influence on microfibre release from the knitted fabrics, with vortex-spun yarns consistently demonstrating lower microfibre release than corresponding ring-spun yarns. This is due to differences in the yarn structure, particularly the level of hairiness which has been shown to correlate with microfibre release both here and in previous studies. Neither yarn nor fibre linear density was found to influence microfibre release for the yarns tested in this study. These results show that changes to the fibre composition and the yarn spinning system would have the greatest influence in terms of reducing microfibre release.
Data availability statement
The original contributions presented in the study are included in the article/Supplementary material, further inquiries can be directed to the corresponding author.
Author contributions
AH: Writing–original draft, Methodology, Investigation, Conceptualization. MS: Writing–review and editing, Supervision, Conceptualization. MT: Writing–review and editing, Supervision, Conceptualization.
Funding
The author(s) declare financial support was received for the research, authorship, and/or publication of this article. This work was supported by The Microfibre Consortium (TMC).
Conflict of interest
The authors declare that the research was conducted in the absence of any commercial or financial relationships that could be construed as a potential conflict of interest.
Publisher’s note
All claims expressed in this article are solely those of the authors and do not necessarily represent those of their affiliated organizations, or those of the publisher, the editors and the reviewers. Any product that may be evaluated in this article, or claim that may be made by its manufacturer, is not guaranteed or endorsed by the publisher.
References
Barella, A. (1956). New concepts of yarn hairiness. J. Text. Inst. Proc. 47, P120–P127. doi:10.1080/19447015608665204
Barella, A. (1957). Yarn hairiness: the influence of twist. J. Text. Inst. Proc. 48, P268–P280. doi:10.1080/19447015708688167
Barella, A., Vega, P. A. A., and Castro, L. (1989). Yarn attrition by abrasion: a comparison of polyester-fibre/cotton blended-fibre yarns spun by different spinning processes. J. Text. Inst. 80, 599–603. doi:10.1080/00405008908658313
Basu, A., and Gotipamul, R. L. (2003). Lint shedding propensity of cotton and blended yarns. Indian J. Fibre Text. Res. 28, 288–294.
Behery, H. M. (2005). “7 - effect of yarn factors on fabric hand,” in Effect of mechanical and physical properties on fabric hand, woodhead publishing series in textiles. Editor H. M. Behery (Sawston, United Kingdom: Woodhead Publishing), 219–238. doi:10.1533/9781845690984.2.219
Belzagui, F., Crespi, M., Álvarez, A., Gutiérrez-Bouzán, C., and Vilaseca, M. (2019). Microplastics’ emissions: microfibers’ detachment from textile garments. Environ. Pollut. 248, 1028–1035. doi:10.1016/j.envpol.2019.02.059
Berruezo, M., Bonet-Aracil, M., Montava, I., Bou-Belda, E., Díaz-García, P., and Gisbert-Payá, J. (2021). Preliminary study of weave pattern influence on microplastics from fabric laundering. Text. Res. J. 91, 1037–1045. doi:10.1177/0040517520965708
Boucher, J., and Friot, D. (2017). Primary microplastics in the oceans: a global evaluation of sources. Gland, Switzerland: IUCN International Union for Conservation of Nature. doi:10.2305/IUCN.CH.2017.01.en
British Standards Institution (1995). Determination of linear density (mass per unit length) by the skein method. London: BSI. Textiles. Yarn from packages.
British Standards Institution (2016). Textiles. Universal system for designating linear density (Tex System) (No. BS ISO 1144:2016). London: BSI.
British Standards Institution (2023). Textiles and textile products - microplastics from textile sources - Part 1: determination of material loss from fabrics during washing (No. BS EN ISO 4484-1). London: BSI.
Browne, M. A., Crump, P., Niven, S. J., Teuten, E., Tonkin, A., Galloway, T., et al. (2011). Accumulation of microplastic on shorelines woldwide: sources and sinks. Environ. Sci. Technol. 45, 9175–9179. doi:10.1021/es201811s
Buhler, G., Rieder, O., and Haussler, W. (1988). Fibre fly, a serious problem for the knitting industry. Knitt. Tech. 10.
Cai, Y., Mitrano, D. M., Heuberger, M., Hufenus, R., and Nowack, B. (2020a). The origin of microplastic fiber in polyester textiles: the textile production process matters. J. Clean. Prod. 267, 121970. doi:10.1016/j.jclepro.2020.121970
Cai, Y., Yang, T., Mitrano, D. M., Heuberger, M., Hufenus, R., and Nowack, B. (2020b). Systematic study of microplastic fiber release from 12 different polyester textiles during washing. Environ. Sci. Technol. 54, 4847–4855. doi:10.1021/acs.est.9b07395
Canoglu, S., and Tanir, S. K. (2009). Studies on yarn hairiness of polyester/cotton blended ring-spun yarns made from different blend ratios. Text. Res. J. 79, 235–242. doi:10.1177/0040517508093780
Carney Almroth, B. M., Åström, L., Roslund, S., Petersson, H., Johansson, M., and Persson, N.-K. (2018). Quantifying shedding of synthetic fibers from textiles; a source of microplastics released into the environment. Environ. Sci. Pollut. Res. 25, 1191–1199. doi:10.1007/s11356-017-0528-7
Celik, S. (2021). Microplastic release from domestic washing. Eur. J. Sci. Technol. doi:10.31590/ejosat.933322
Cesa, F. S., Turra, A., Checon, H. H., Leonardi, B., and Baruque-Ramos, J. (2020). Laundering and textile parameters influence fibers release in household washings. Environ. Pollut. 257, 113553. doi:10.1016/j.envpol.2019.113553
Choi, S., Kwon, M., Park, M.-J., and Kim, J. (2021a). Analysis of microplastics released from plain woven classified by yarn types during washing and drying. Polymers 13, 2988. doi:10.3390/polym13172988
Choi, S., Kwon, M., Park, M.-J., and Kim, J. (2021b). Characterization of microplastics released based on polyester fabric construction during washing and drying. Polymers 13, 4277. doi:10.3390/polym13244277
Ciechañska, D., and Nousiainen, P. (2005). “Cellulosic fibres and fabric processing,” in Biodegradable and sustainable fibres (Amsterdam, Netherlands: Elsevier), 111–156. doi:10.1533/9781845690991.111
Das, D. (2004). Raw material characteristics vis-à-visrotor spinning technology: a review. Fibres Text. - Vlákna Text. 4, 94–98.
De Falco, F., Cocca, M., Guarino, V., Gentile, G., Ambrogi, V., Ambrosio, L., et al. (2019a). Novel finishing treatments of polyamide fabrics by electrofluidodynamic process to reduce microplastic release during washings. Polym. Degrad. Stab. 165, 110–116. doi:10.1016/j.polymdegradstab.2019.05.001
De Falco, F., Di Pace, E., Cocca, M., and Avella, M. (2019b). The contribution of washing processes of synthetic clothes to microplastic pollution. Sci. Rep. 9, 6633. doi:10.1038/s41598-019-43023-x
De Falco, F., Gullo, M. P., Gentile, G., Di Pace, E., Cocca, M., Gelabert, L., et al. (2018). Evaluation of microplastic release caused by textile washing processes of synthetic fabrics. Environ. Pollut. 236, 916–925. doi:10.1016/j.envpol.2017.10.057
Elhawary, I. A. (2015). “Chapter 9 - fibre to yarn: staple-yarn spinning,” in Textiles and fashion: materials, design and technology (Cambridge: Woodhead Publishing, Ltd, in association with the Textile Institute), 191–212.
Elmogahzy, Y., and Farag, R. (2018). “Tensile properties of cotton fibers,” in Handbook of properties of textile and technical fibres (Amsterdam, Netherlands: Elsevier), 223–273. doi:10.1016/B978-0-08-101272-7.00007-9
Fink, H.-P., Weigel, P., Purz, H. J., and Ganster, J. (2001). Structure formation of regenerated cellulose materials from NMMO-solutions. Prog. Polym. Sci. 26, 1473–1524. doi:10.1016/S0079-6700(01)00025-9
Gaylarde, C., Baptista-Neto, J. A., and da Fonseca, E. M. (2021). Plastic microfibre pollution: how important is clothes’ laundering? Heliyon 7, e07105. doi:10.1016/j.heliyon.2021.e07105
Goswami, P., Blackburn, R. S., El-Dessouky, H. M., Taylor, J., and White, P. (2009). Effect of sodium hydroxide pre-treatment on the optical and structural properties of lyocell. Eur. Polym. J. 45, 455–465. doi:10.1016/j.eurpolymj.2008.10.030
Graupner, N., Schmidt, S., Gauss, C., and Müssig, J. (2023). Making positive use of the fibrillation of lyocell fibres in composite materials. Compos. Part C Open Access 11, 100359. doi:10.1016/j.jcomc.2023.100359
Hearle, J. W. S. (2001). “Physical structure and fibre properties,” in Regenerated cellulose fibres (Amsterdam, Netherlands: Elsevier), 199–234. doi:10.1533/9781855737587.199
Hossain, Md.S., Islam, Md.M., Dey, S. C., and Hasan, N. (2021). An approach to improve the pilling resistance properties of three thread polyester cotton blended fleece fabric. Heliyon 7, e06921. doi:10.1016/j.heliyon.2021.e06921
Huh, Y., Young, R. K., and Oxenham, W. (2002). Analyzing structural and physical properties of ring, rotor, and friction spun yarns. Text. Res. J. 72, 156–163. doi:10.1177/004051750207200212
Hurley, R. R., Woodward, J. C., and Rothwell, J. J. (2017). Ingestion of microplastics by freshwater tubifex worms. Environ. Sci. Technol. 51, 12844–12851. doi:10.1021/acs.est.7b03567
Jabbar, A., Palacios-Marín, A. V., Ghanbarzadeh, A., Yang, D., and Tausif, M. (2022). Impact of conventional and modified ring-spun yarn structures on the generation and release of fragmented fibers (microfibers) during abrasive wear and laundering. Text. Res. J. 93, 1099–1112. doi:10.1177/00405175221127709
Jabbar, A., and Tausif, M. (2023). Investigation of ring, airjet and rotor spun yarn structures on the fragmented fibers (microplastics) released from polyester textiles during laundering. Text. Res. J. 93, 5017–5028. doi:10.1177/00405175231191785
Kärkkäinen, N., and Sillanpää, M. (2020). Quantification of different microplastic fibres discharged from textiles in machine wash and tumble drying. Environ. Sci. Pollut. Res. 28, 16253–16263. doi:10.1007/s11356-020-11988-2
Kelly, M. R., Lant, N. J., Kurr, M., and Burgess, J. G. (2019). Importance of water-volume on the release of microplastic fibers from laundry. Environ. Sci. Technol. 53, 11735–11744. doi:10.1021/acs.est.9b03022
Kim, S., Cho, Y., and Park, C. H. (2022). Effect of cotton fabric properties on fiber release and marine biodegradation. Text. Res. J. 92, 2121–2137. doi:10.1177/00405175211068781
Koo, Y. S. (2003). Yarn hairiness affecting fluff generation. Fibers Polym. 4, 119–123. doi:10.1007/bf02875458
Krupincová, G., and Meloun, M. (2013). Yarn hairiness versus quality of yarn. J. Text. Inst. 104, 1312–1319. doi:10.1080/00405000.2013.800377
Kumpikaitė, E., Tautkutė-Stankuvienė, I., Simanavičius, L., and Petraitienė, S. (2021). The influence of finishing on the pilling resistance of linen/silk woven fabrics. Materials 14, 6787. doi:10.3390/ma14226787
Kutralam-Muniasamy, G., Pérez-Guevara, F., Elizalde-Martínez, I., and Shruti, V. C. (2020). An overview of recent advances in micro/nano beads and microfibers research: critical assessment and promoting the less known. Sci. Total Environ. 740, 139991. doi:10.1016/j.scitotenv.2020.139991
Lant, N. J., Hayward, A. S., Peththawadu, M. M. D., Sheridan, K. J., and Dean, J. R. (2020). Microfiber release from real soiled consumer laundry and the impact of fabric care products and washing conditions. PLOS ONE 15, e0233332. doi:10.1371/journal.pone.0233332
Lawrence, C. A., and Mohamed, S. A. (1996). Yam and knitting parameters affecting fly during weft knitting of staple yarns. Text. Res. J. 66, 694–704. doi:10.1177/004051759606601105
Lenz, J., Schurz, J., and Wrentschur, E. (1993). Properties and structure of solvent-spun and viscose-type fibres in the swollen state. Colloid Polym. Sci. 271, 460–468. doi:10.1007/BF00657390
Liu, J., Liang, J., Ding, J., Zhang, G., Zeng, X., Yang, Q., et al. (2021). Microfiber pollution: an ongoing major environmental issue related to the sustainable development of textile and clothing industry. Environ. Dev. Sustain. 23, 11240–11256. doi:10.1007/s10668-020-01173-3
Liu, J., Yang, Y., Ding, J., Zhu, B., and Gao, W. (2019). Microfibers: a preliminary discussion on their definition and sources. Environ. Sci. Pollut. Res. 26, 29497–29501. doi:10.1007/s11356-019-06265-w
Liu, J., Zhu, B., An, L., Ding, J., and Xu, Y. (2023). Atmospheric microfibers dominated by natural and regenerated cellulosic fibers: explanations from the textile engineering perspective. Environ. Pollut. 317, 120771. doi:10.1016/j.envpol.2022.120771
Majumdar, A. (2010). “Yarn hairiness and its reduction,” in Technical textile yarns (Amsterdam, Netherlands: Elsevier), 112–139. doi:10.1533/9781845699475.1.112
Michud, A., Hummel, M., and Sixta, H. (2016). Influence of process parameters on the structure formation of man-made cellulosic fibers from ionic liquid solution. J. Appl. Polym. Sci. 133, 43718. doi:10.1002/app.43718
Miyake, H., Gotoh, Y., Ohkoshi, Y., and Nagura, M. (2000). Tensile properties of wet cellulose. Polym. J. 32, 29–32. doi:10.1295/polymj.32.29
Moriam, K., Sawada, D., Nieminen, K., Hummel, M., Ma, Y., Rissanen, M., et al. (2021). Towards regenerated cellulose fibers with high toughness. Cellulose 28, 9547–9566. doi:10.1007/s10570-021-04134-9
Mortimer, S. A., and Peguy, A. A. (1996). The influence of air-gap conditions on the structure formation of lyocell fibers. J. Appl. Polym. Sci. 60, 1747–1756. doi:10.1002/(SICI)1097-4628(19960606)60:10<1747::AID-APP28>3.0.CO;2-#
Mortimer, S. A., and Péguy, A. A. (1996). Methods for reducing the tendency of Lyocell fibers to fibrillate. J. Appl. Polym. Sci. 60, 305–316. doi:10.1002/(SICI)1097-4628(19960418)60:3<305::AID-APP3>3.0.CO;2-P
Oxtoby, E. (1963). 44—An investigation into the formation of fly waste during worsted cap spinning. J. Text. Inst. Trans. 54, T501–T512. doi:10.1080/19447026308660202
Özkan, İ., and Gündoğdu, S. (2021). Investigation on the microfiber release under controlled washings from the knitted fabrics produced by recycled and virgin polyester yarns. J. Text. Inst. 112, 264–272. doi:10.1080/00405000.2020.1741760
Palacios-Marín, A. V., Jabbar, A., and Tausif, M. (2022). Fragmented fiber pollution from common textile materials and structures during laundry. Text. Res. J. 92, 2265–2275. doi:10.1177/00405175221090971
Parajuli, P., Acharya, S., Rumi, S. S., Hossain, Md.T., and Abidi, N. (2021). “Regenerated cellulose in textiles: rayon, lyocell, modal and other fibres,” in Fundamentals of natural fibres and textiles, the textile institute book series (Sawston, United Kingdom: Woodhead Publishing Limited), 87–110.
Patnaik, A., Rengasamy, R. S., Ishtiaque, S. M., and Ghosh, A. (2007). Hairiness of spun yarns and their reduction using air-nozzle in winding. J. Text. Inst. 98, 243–249. doi:10.1080/00405000701502743
Periyasamy, A. P. (2021). Evaluation of microfiber release from jeans: the impact of different washing conditions. Environ. Sci. Pollut. Res. 28, 58570–58582. doi:10.1007/s11356-021-14761-1
Pinlova, B., Hufenus, R., and Nowack, B. (2022). Systematic study of the presence of microplastic fibers during polyester yarn production. J. Clean. Prod. 363, 132247. doi:10.1016/j.jclepro.2022.132247
Pirc, U., Vidmar, M., Mozer, A., and Kržan, A. (2016). Emissions of microplastic fibers from microfiber fleece during domestic washing. Environ. Sci. Pollut. Res. 23, 22206–22211. doi:10.1007/s11356-016-7703-0
Raja Balasaraswathi, S., and Rathinamoorthy, R. (2022). Effect of fabric properties on microfiber shedding from synthetic textiles. J. Text. Inst. 113, 789–809. doi:10.1080/00405000.2021.1906038
Rathinamoorthy, R., and Raja Balasaraswathi, S. (2022a). “Domestic laundry—a major cause of microfiber shedding,” in Microfiber pollution, sustainable textiles: production, processing, manufacturing and chemistry. Editors R. Rathinamoorthy, and S. Raja Balasaraswathi (Singapore: Springer Nature), 107–149. doi:10.1007/978-981-19-4185-6_4
Rathinamoorthy, R., and Raja Balasaraswathi, S. (2022b). Investigations on the impact of handwash and laundry softener on microfiber shedding from polyester textiles. J. Text. Inst. 113, 1428–1437. doi:10.1080/00405000.2021.1929709
Rebelein, A., Int-Veen, I., Kammann, U., and Scharsack, J. P. (2021). Microplastic fibers — underestimated threat to aquatic organisms? Sci. Total Environ. 777, 146045. doi:10.1016/j.scitotenv.2021.146045
Ruppenicker, G. F., and Lofton, J. T. (1979). Factors affecting the lint shedding of cotton knitting yams. Text. Res. J. 49, 681–685. doi:10.1177/004051757904901201
Sharma, A., Wankhede, P., Samant, R., Nagarkar, S., Thakre, S., and Kumaraswamy, G. (2021). Process-induced microstructure in viscose and lyocell regenerated cellulose fibers revealed by SAXS and SEM of acid-etched samples.
Sillanpää, M., and Sainio, P. (2017). Release of polyester and cotton fibers from textiles in machine washings. Environ. Sci. Pollut. Res. 24, 19313–19321. doi:10.1007/s11356-017-9621-1
Sinclair, R. (2015). “Understanding textile fibres and their properties,” in Textiles and fashion (Amsterdam, Netherlands: Elsevier), 3–27. doi:10.1016/B978-1-84569-931-4.00001-5
Tiffin, L., Hazlehurst, A., Sumner, M., and Taylor, M. (2022). Reliable quantification of microplastic release from the domestic laundry of textile fabrics. J. Text. Inst. 113, 558–566. doi:10.1080/00405000.2021.1892305
Tomaney, M. (2015). “Sustainable textile production,” in Textiles and fashion (Amsterdam, Netherlands: Elsevier), 547–560. doi:10.1016/B978-1-84569-931-4.00022-2
Udomkichdecha, W., Chiarakorn, S., and Potiyaraj, P. (2002). Relationships between fibrillation behavior of lyocell fibers and their physical properties. Text. Res. J. 72, 939–943. doi:10.1177/004051750207201101
Vassilenko, E., Watkins, M., Chastain, S., Mertens, J., Posacka, A. M., Patankar, S., et al. (2021). Domestic laundry and microfiber pollution: exploring fiber shedding from consumer apparel textiles. PLOS ONE 16, e0250346. doi:10.1371/journal.pone.0250346
Wang, X. (1999). Recent research on yarn hairiness testing and reduction: Part - reduction of yarn hairiness. Res. J. Text. Appar. 3, 1–8. doi:10.1108/RJTA-03-01-1999-B001
White, P. (2001). “Lyocell: the production process and market development,” in Regenerated cellulose fibres (Amsterdam, Netherlands: Elsevier), 62–87. doi:10.1533/9781855737587.62
Yang, L., Qiao, F., Lei, K., Li, H., Kang, Y., Cui, S., et al. (2019). Microfiber release from different fabrics during washing. Environ. Pollut. 249, 136–143. doi:10.1016/j.envpol.2019.03.011
Yuksekkaya, M. E. (2010). Fiber fly generation of 100% acrylic yarns during weaving. Text. Res. J. 80, 508–515. doi:10.1177/0040517509340604
Zambrano, M. C., Pawlak, J. J., Daystar, J., Ankeny, M., Cheng, J. J., and Venditti, R. A. (2019). Microfibers generated from the laundering of cotton, rayon and polyester based fabrics and their aquatic biodegradation. Mar. Pollut. Bull. 142, 394–407. doi:10.1016/j.marpolbul.2019.02.062
Keywords: microfibre pollution, microplastics, textiles, yarn characteristics, domestic laundering
Citation: Hazlehurst A, Sumner M and Taylor M (2024) Investigating the influence of yarn characteristics on microfibre release from knitted fabrics during laundering. Front. Environ. Sci. 12:1340229. doi: 10.3389/fenvs.2024.1340229
Received: 17 November 2023; Accepted: 08 March 2024;
Published: 20 March 2024.
Edited by:
Thomas Stanton, Loughborough University, United KingdomReviewed by:
Aminoddin Haji, Yazd University, IranMiranda Prendergast-Miller, Northumbria University, United Kingdom
Shanshan Li, Qingdao Agricultural University, China
Copyright © 2024 Hazlehurst, Sumner and Taylor. This is an open-access article distributed under the terms of the Creative Commons Attribution License (CC BY). The use, distribution or reproduction in other forums is permitted, provided the original author(s) and the copyright owner(s) are credited and that the original publication in this journal is cited, in accordance with accepted academic practice. No use, distribution or reproduction is permitted which does not comply with these terms.
*Correspondence: Alice Hazlehurst, sd16ad@leeds.ac.uk