[팜뉴스=최선재 기자] '스마트 팩토리'가 제약바이오 업계의 대세로 떠오르고 있다. 스마트 팩토리는 설비에 사물인터넷(IoT), 빅데이터 등을 적용해 데이터를 실시간으로 수집·분석하는 공장이다. 최근 식약처가 의약품 GMP 기준에 QbD(설계기반 품질고도화) 도입을 시사하면서 스마트 팩토리 구축 필요성이 더욱 커졌다. 제약업계의 이목이 스마트 팩토리를 구축한 기업을 향해 쏠린 배경이다.
그렇다면 스마트 팩토리 구축의 장점은 뭘까. 보령 최병인 품질본부 DI팀장은 14일 열린 "제약 스마트 공장 우수 사례 공유" 세미나에서 보령 예산 공장 설립 뒷이야기와 노하우를 공개했다. 그는 2019년 당시 모든 공정에 ‘스마트 팩토리’를 갖춘 예산 공장의 밑그림을 설계한 주인공이다.
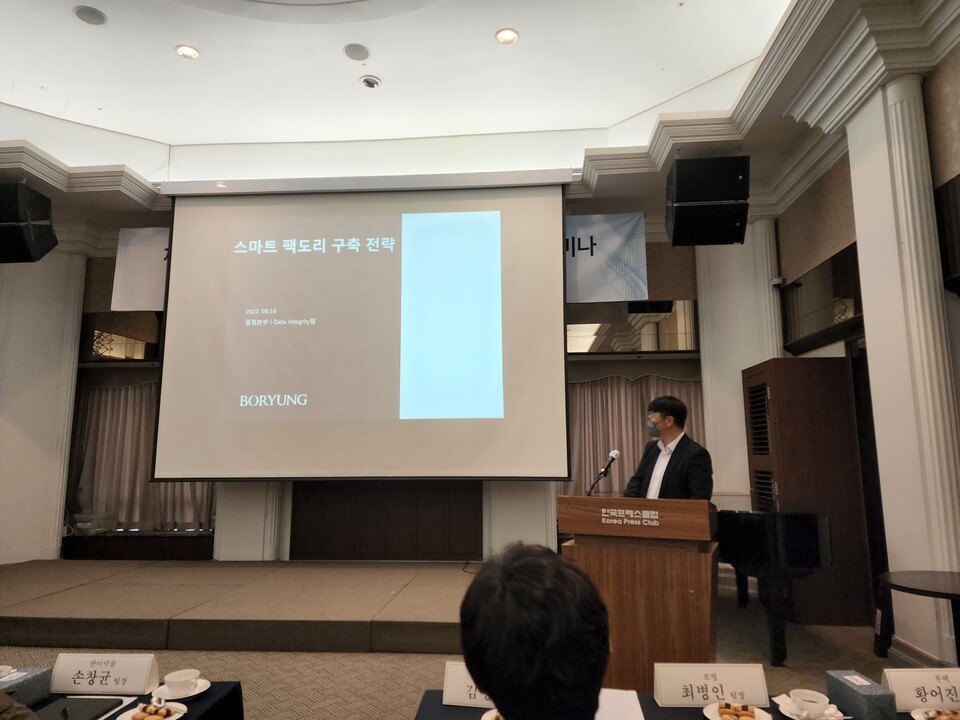
# QbD 기초 데이터 수립과 데이터 완전성 확보
저는 보령의 예산 공장 건설 때부터 참여해서 스마트 팩토리 관련 자동화 시스템 전체 콘셉트를 설계했다. 현재 보령의 자동화시스템을 운영 중이고 저희는 MES(스마트 공장의 기반으로 제조 현장 운영 시스템, Manufacturing Execution System)과 연관된 전반적인 것을 검토하고 장애가 발생하면 조치하고 있다.
제약 산업에서 스마트 공장을 도입하는 목표는 QbD다. QbD를 위해서는 기초적인 데이터들이 많이 필요하다. 즉 라이브러리를 구축해야 그 자료를 가지고 QbD의 기초가 되는 데이터를 활용할 수 있다. 과거에 저희들은 기초 자료를 수기로 관리하거나 엑셀로 관리했지만 자동화시스템 도입으로 DI(데이터 완전성, Data Integrity)과 정확성을 확보했다.
스마트 공장 도입은 두 가지 측면에서 효과가 높았다. 데이터를 실시간으로 기록하고 이를 토대로 제조 공정을 승인하는 것은 물론 '휴먼 에러(인간 오류)'가 감소 중이다. 특히 작업자들의 인위적인 실수가 감소해서 공장의 안정화를 높일 수 있었다. 지금은 스마트 자동화 시스템 도입으로 전부 종이 문서가 없어지고 있다.
# 데이터 완전성 확보 = 신속하고 정확한 '일탈 대응'
앞에서 언급했지만 스마트 팩토리 자동화 시스템은 실시간 기록 등 모든 데이터에 대한 DI 확보가 가능하다. 이는 데이터를 거짓으로 조작할 수 없다는 뜻이다. 인위적으로 수치를 바꾸면 기록이 남는다. 데이터 완전성 확보가 가능하다는 것은 곧 모든 데이터가 신뢰성을 지닌다는 뜻으로 해석할 수 있다.
저희가 의약품 제조 공정에서 발생한 일탈 상황에 능동적이고 정확한 대응이 가능한 이유다. 일탈 등 어떤 상황이 발생하면 실시간으로 데이터 추적이 가능하다. 자동화 시스템을 통해 과거 데이터 불러오면, 해당 데이터에 신뢰성이 있기 때문에 일탈이나 어떤 상황에 대해 명확한 진단이 가능하다.
옛날에는 사람이 수기로 문서를 발행하고 수작업으로 일일이 작성했다. 하지만 제 경험상 실시간으로 작성을 하면서 작업하기는 상당히 힘들다. 인위적인 오류(휴먼 에러)가 더 많이 발생하고 데이터 신뢰성이 없어서 이슈가 생겼을 때 정확한 진단이 어렵다.
사람이 전부 올리고 검토를 거쳐 마감을 했는데 이슈가 생기면 과거 이력을 되짚어봐야 하는데 "과연 신뢰할 수 있는 데이터인가"하는 의문이 생기는 이유다. 일일이 문서를 전부 뒤져야 하는 불편함도 있다. 스마트 팩토리를 도입하면 실시간으로 과거 데이터가 조회되고 관계자들이 전부 바로 리뷰가 가능하다.
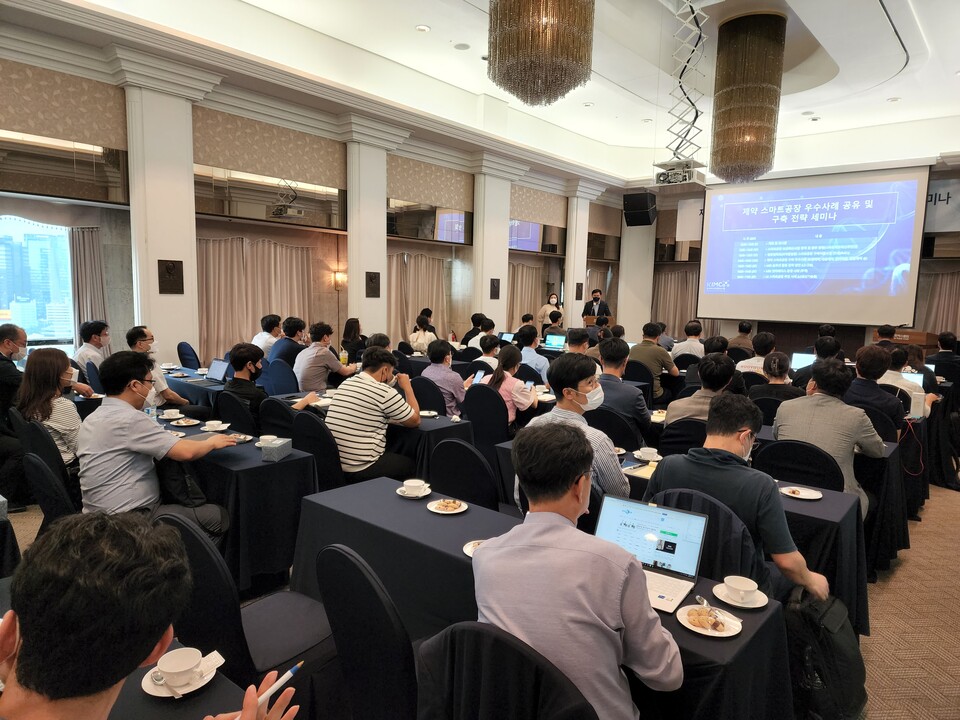
# '예방 정비'와'실사' 대비 가능
스마트 팩토리는 '예방 정비'도 가능하다. 장비가 자동으로 데이터를 취합하면 MES나 또 다른 대시보드를 통해 현장 상황을 실시간으로 모니터링할 수 있다. 모니터링한 데이터들이 축적되고 이를 분석하면 장비들이나 여러 상황을 예측할 수 있는 시스템이 스마트 팩토리다.
"장비를 이쯤 사용하니까 이런 증상이 나타나더라"는 데이터 추이가 나오기 때문이다. 과거에 필터 교체 주기를 일정 기간으로 가져갔다면 스마트 팩토리 시스템은 쌓인 데이터에서 올라오는 수치를 토대로 교체 주기를 맞춤형으로 정할 수 있다. 실제 교체가 필요없는 필터에 대한 기간을 늘리면 원가가 절감되고 나아가 데이터를 가지고 사전에 예방 정비를 할 수 있는 경우도 생긴다.
이뿐만이 아니다. 저희는 한국혁신의약품컨소시엄의 지원을 받아 최근 실시간 데이터 기반 에너지 데이터 관리 시스템 (EDMS)을 도입했다. 도입 당시 여러 가지 방향을 생각했는데 그중에 하나가 각 메인 작업장에 MES 단말기를 두는 것이다. 단말기에서 화면을 띄워서 실시간으로 SOP(표준작업절차서,Standard Operating Procedure)를 볼 수 있도록 했다.
현장의 최신의 SOP를 작업자가 실시간으로 볼 수 있고 접할 수 있다는 얘기다. 현장에 실사자들이 와서 SOP가 비치돼있느냐고 물었을 때 해당 화면을 뛰워서 보여줄 수 있다. 단순히 보는 것이기 때문에 관리 권한이 없더라도 가능하다. 감사자들이 실사를 나왔을 때 적극적으로 대응이 가능한 이유다.
# '생산, 품질, 경영' 삼박자 갖춘 '스마트 팩토리'
종합적인 의견을 말씀드리면 자동화 시스템으로 생산 측면에서는 작업자 실수, 즉 휴먼 에러를 최소화할 수 있고, 현장의 서류 업무를 없앨 수 있다. 라벨, 로그북 작성 등은 생산 입장에서 상당한 스트레스를 주기 때문에 더욱 효율적이다. 뿐만 아니라 문서에 대한 분실이나 기록 누락 방지도 가능하다.
품질 측면에서는 실사 준비 기간을 단축할 수 있다. 데이터 신뢰를 확보한 상황이기 때문에 품질 사고 발생시에도 정확한 원인 파악이 가능하다. 일탈이 발생했을 때도 다르지 않다. 작업자 실수로 인한 품질사고도 원천적으로 예방 가능한 구조다.
경영 측면에서는 모든 생산적인 현황을 한눈에 파악해서 공장 상황 또는 생산 현황에 대한 트렌드 분석이 가능하다. 감사나 시찰에 실시간으로 대응할 수 있다는 것도 이점이다. 뿐만 아니라 기록서 검토 시간을 단축하고 실시간으로 생산 현장 상황을 파악할 수 있다. 데이터들이 쌓이면 생산적인 지표 등 데이터를 활용해서 연간 품질 평가를 진행하는 것도 수월하다.
관련기사
개의 댓글
댓글 정렬
그래도 삭제하시겠습니까?